与Dolomiti进行了富有成效的合作
用有机种植的苹果和梨制成的全天然果汁、果肉和酱深受意大利消费者的喜爱。但这个行业竞争激烈,生产商不得不关注自己的利润率。
日期 2024-03-01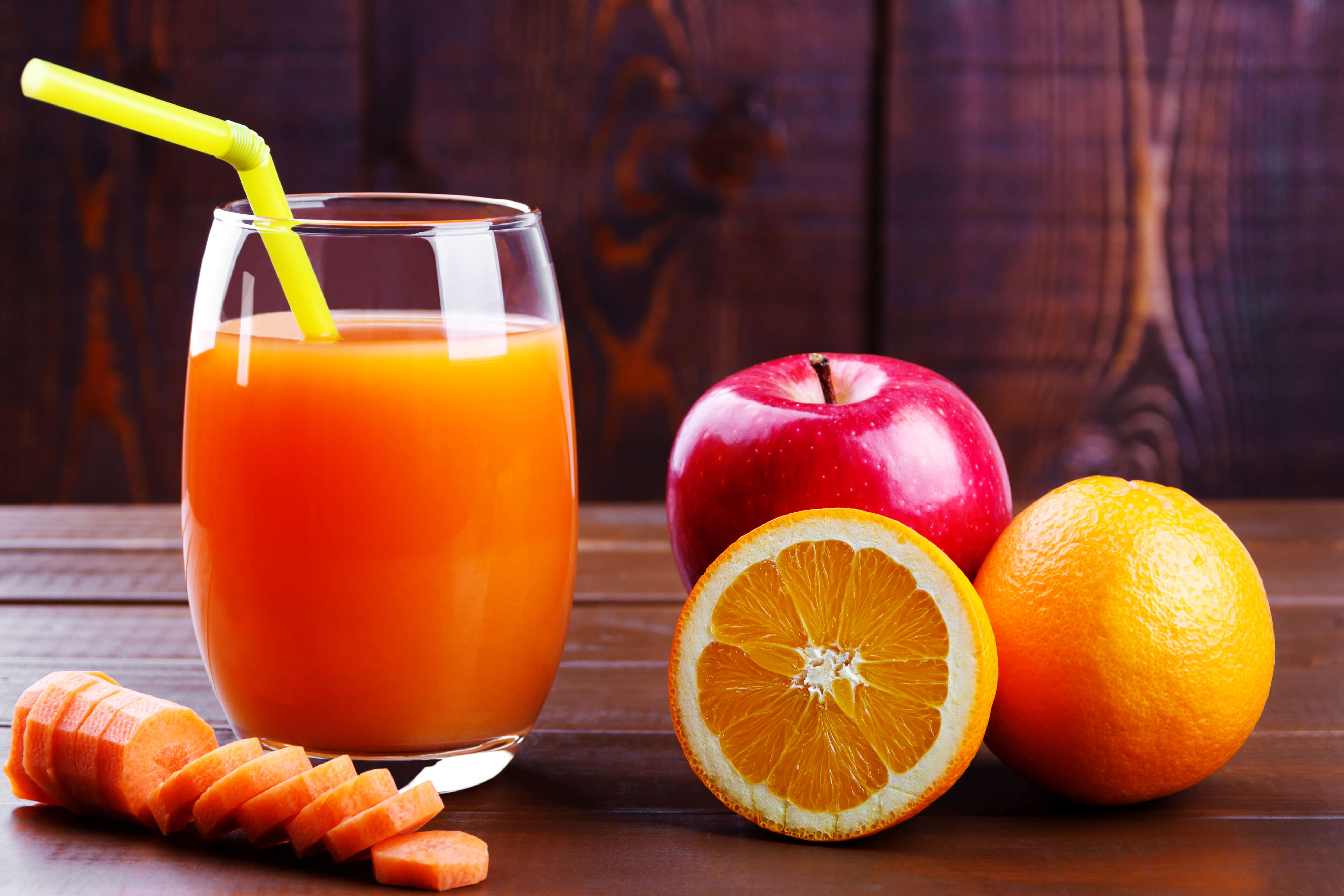
Back in 2018, Dolomiti was using a large tubular heat exchanger for the enzymatic deactivation step of its production. However, operators noticed that fruit particles were sticking to the tubes. The sugar got burned onto the metal surfaces, reducing the heat exchangers’ efficiency and making it difficult to clean. They also observed a pressure drop of up to 16 bars, which presented a challenge for their pumps, as well as increasing power consumption.
Distributor suggests plate heat exchanger
To resolve these issues, Dolomiti started looking for a new type of heat treatment technology. They sought advice from Tekna Parma, Alfa Laval’s local Italian partner, stating their main ambitions: to reduce pressure drop, lower energy consumption and make cleaning easier. On Tekna Parma’s advice, they decided to try out an Alfa Laval plate heat exchanger with wider gaps.
Two down; one to go
Using this new type of plate heat exchanger increased heat recovery, enabling a 45% reduction in steam consumption. Moreover, it lowered the pressure drop, cutting electricity consumption with 10–15%. However, Dolomiti’s production manager still wanted to improve the cleanability of the plates. He clearly stated the importance of this requirement in discussions with Tekna Parma and Alfa Laval’s channel manager, Jakob Worsoe, and the three decided to work together to develop a new solution.
Collaborative product development
“Listening carefully to the customer’s needs and ambitions proved fruitful for all involved”, says Industrialization project manager Clemens Wictor. “Sometimes it’s very helpful to have a new pair of eyes on our products. We can then study the details and decide whether or not it’s possible to develop a solution to the customer’s problem.”
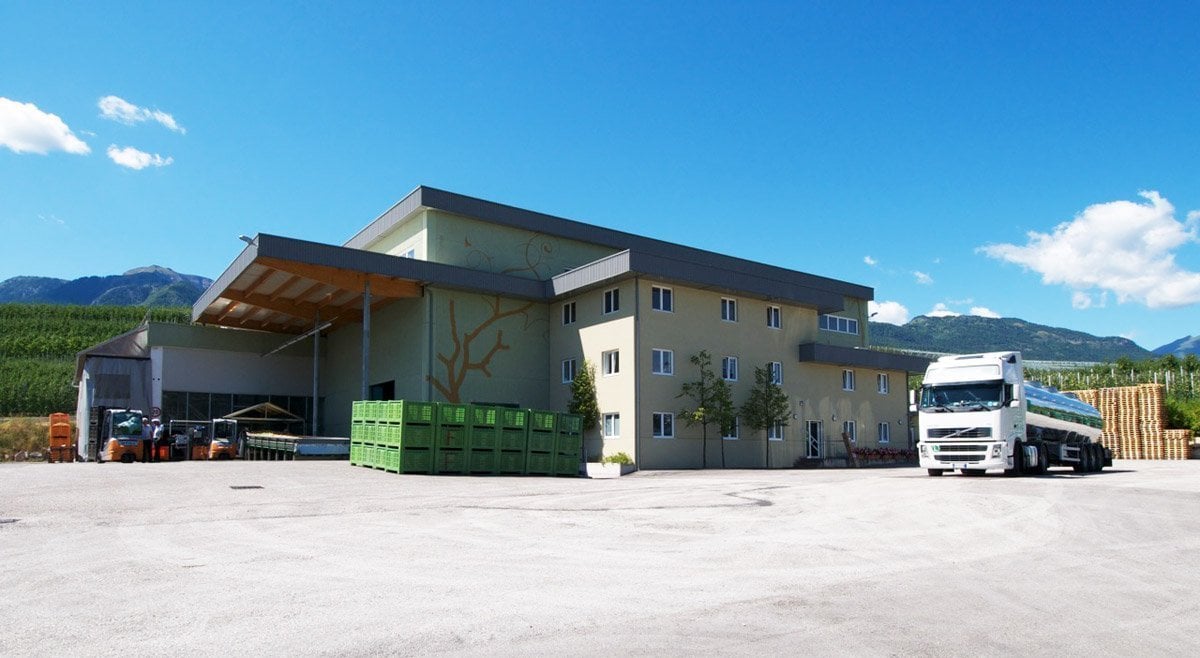
The test results on Alfa Laval’s modified heat exchanger plates were good, and a decision was taken to implement these in the new all hygienic WideGap plates. “In fact, this collaboration laid the foundation for the creation of Alfa Laval’s Hygienic line HL8-WG plates, which take hygiene a step further,” concludes Clemens.
New factory, new decision
Two years later, when Dolomiti was building a new production plant, they needed to decide which kind of heat exchangers to invest in: the old-style tubular heat exchangers or Alfa Laval’s WideGap plate heat exchanger technology?
Encouraged by Clemens and Jakob and the positive experience, they opted for the new design, and they haven’t regretted their decision for a moment! Says Dolomiti, “Thanks to the dramatic improvement in energy consumption, our investment paid for itself within a year, and the heat exchangers have been performing well for over three years.”
A major reduction in energy consumption
Dolomiti now has four production lines, all of which use Alfa Laval’s state-of-the-art WideGap heat exchanger technology, and the plant produces up to 250 tonnes of all-natural, high-quality fruit juices, pulps and purées every day. Altogether, the company has processed more than 80,000 tonnes of fruit using our heat exchangers. Product quality and cleanliness have improved; pressure drop is down from 16 to 9 bars, and the company has even gained some floor space since the new heat exchangers have a smaller footprint than the old equipment. But the biggest impact of the new heat exchangers has been on energy costs. “With approximately 10–15% lower electricity consumption, combined with product-to-product heat recover of reduced steam between 45–55%, we calculated that we can save about €400,000 per year on energy” says Dolomiti.
突出的技术
Energy savings
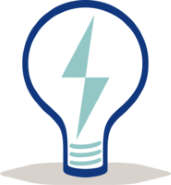
45% lower energy consumption
Technology shift

Replaced old-style technology with new solution
Energy cost savings
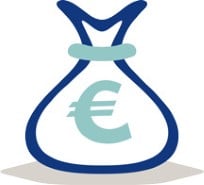
Energy cost savings of €400,000 per year
Emissions savings
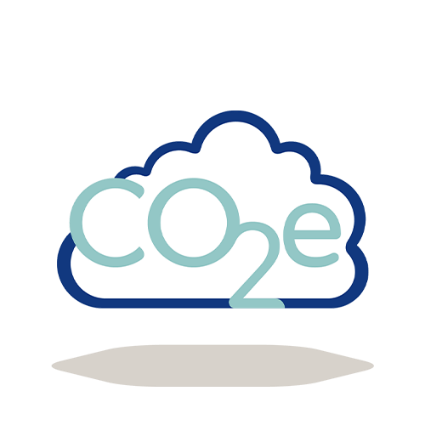
Savings of 500 tonnes of CO2